Tailored Packaging Devices Repair Service Provider to Suit Your Distinct Business Demands
In today's competitive market, organizations have to ensure their packaging procedures run effortlessly, and customized repair solutions for equipment are critical in accomplishing this. This discussion intends to uncover the nuanced benefits of customized repair strategies.
Comprehending Your Tools Demands
To successfully attend to the repair service and upkeep of product packaging devices, it is critical to acquire a comprehensive understanding of your equipment needs (packaging equipment repair services). This involves analyzing the details sorts of equipment being used and identifying their duties within your manufacturing line. Acknowledging these aspects permits you to prioritize maintenance jobs and allot resources successfully, decreasing downtime and ensuring smooth procedures
An in-depth supply of your equipment, including make, version, age, and maintenance background, develops the cornerstone of this understanding. This data assists in educated decision-making relating to repair services and upgrades, guaranteeing that interventions are both prompt and cost-effective. In addition, recognizing the operational demands positioned on each tool helps in predicting wear and tear patterns, therefore allowing more precise organizing of preventative upkeep.
Collaborating with knowledgeable professionals that can give expert analyses and recommendations is additionally essential in fine-tuning your equipment monitoring method. Ultimately, a comprehensive grip of your tools needs not only enhances performance but additionally prolongs the lifespan of your machinery, protecting your investment.
Advantages of Personalized Repair Work Solutions
Custom-made repair services provide a tailored method to fixing and maintaining packaging tools, guaranteeing services that fit the special demands of each organization. This bespoke technique provides myriad benefits, enhancing operational effectiveness and lessening downtime. By recognizing the particular equipment and procedures of a company, personalized solutions can resolve concerns more efficiently than common options, making certain that fixings are straightened with operational goals and process characteristics.
Additionally, these solutions promote much better source management. Tailored repair service plans help anticipate maintenance needs, permitting businesses to allocate resources more effectively and minimize unforeseen costs. This aggressive strategy not just extends devices life expectancy but also maximizes performance, protecting against constant failures and fostering a much more trustworthy manufacturing atmosphere.
Furthermore, customized repair solutions enhance the flexibility of organizations to evolving market problems. As product packaging technologies breakthrough, having a fixing solution in harmony with a business's special configuration guarantees quick adjustment to brand-new tools and procedures. This agility is critical for preserving competitive advantage and customer contentment. Additionally, tailored service promotes a better partnership with repair work carriers, making sure quicker reaction times and more reliable interaction, inevitably leading to improved service high quality and company development.
Key Elements of Tailored Solutions
A well-crafted customized remedy for packaging tools repair is built upon a number of important elements that guarantee efficiency and integrity. To start with, a detailed evaluation of the equipment is essential. This includes detecting the root reason of any kind of functional issues and understanding the certain demands of the equipment, which prepares for developing a precise repair service method.
Second of all, making use of high-grade, suitable components is paramount. Choosing elements that line up with the initial devices requirements not just boosts performance yet also lengthens the life-span of the machinery. This attention to detail decreases the threat of future break downs and makes sure smooth operation.
Another essential element is the application of a personalized upkeep strategy. packaging equipment repair services. Preventive steps and regular assessments customized to the tools's special demands can dramatically decrease downtime and boost efficiency
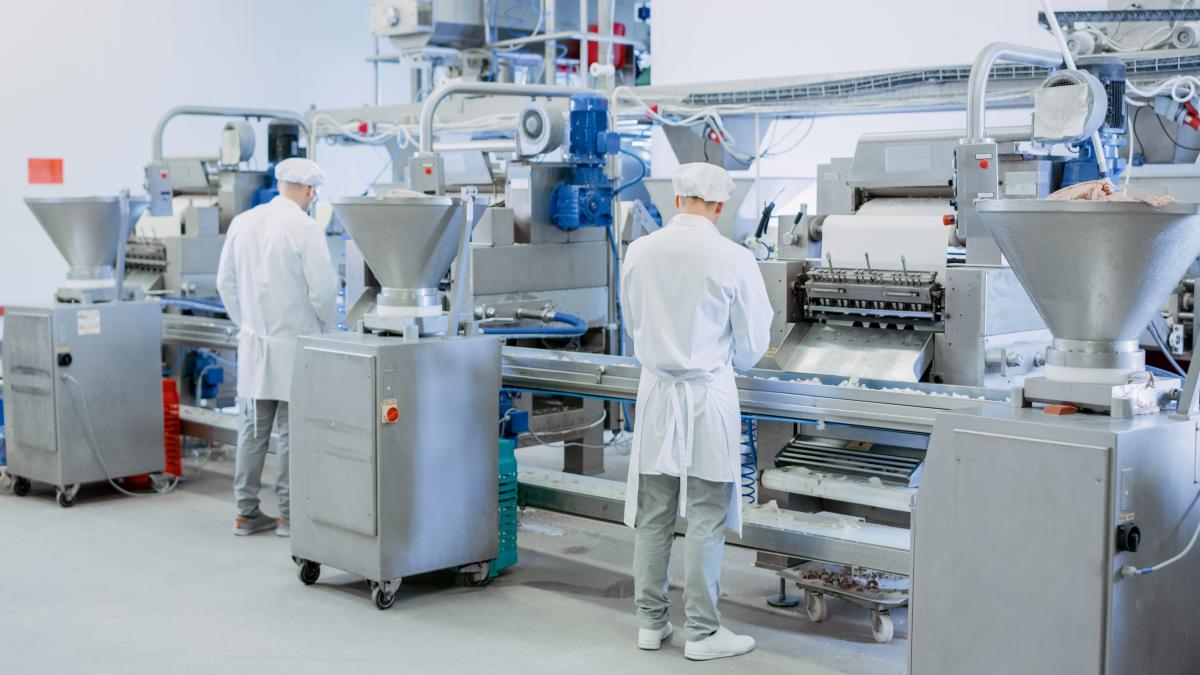
Integrating these components right into a tailored repair service important link not only addresses immediate issues yet also offers long-lasting benefits, enhancing overall productivity and cost-effectiveness for services.
Choosing the Right Service Provider
Choosing the appropriate company for product packaging equipment repair is a crucial decision that can dramatically influence an organization's functional performance and cost administration. A trustworthy company makes certain timely repair work and upkeep, minimizing downtime and avoiding prospective production delays. When choosing a provider, businesses need to think about several important aspects to guarantee they choose a companion that lines up with their certain demands.
To start with, expertise and experience in managing similar devices are essential. A service copyright with a tried and tested performance history in the product packaging market can supply remedies and insights tailored to one-of-a-kind business difficulties. Recommendations and study from previous clients can offer useful evidence of their capabilities.
Second of all, evaluate the supplier's responsiveness and accessibility. packaging equipment repair services. A suitable companion must use adaptable service alternatives, consisting of emergency situation repair service services, to deal with urgent needs quickly. This makes sure very little disruption to procedures and maintains productivity levels
In addition, take into consideration the range of solutions provided. A comprehensive supplier must not only supply repairs however additionally preventive upkeep and technical assistance. This all natural method can streamline procedures and foster lasting partnerships.

Optimizing Devices Lifespan
Effective tools upkeep techniques are as essential as picking the ideal provider when it concerns making the most of the life expectancy of product packaging devices. Normal maintenance, when executed correctly, extends the functional life of machinery by protecting against unexpected failures and reducing repair service expenses. This includes executing a structured upkeep timetable that includes regular inspections, timely lubrication, and substitute of damaged parts. Such aggressive steps guarantee more information that equipment features at peak performance, thus minimizing the danger of pricey downtime.
In addition, investing in training for your technical personnel can substantially influence the long life of the equipment. Proficient workers can determine potential concerns early, permitting speedy rehabilitative activities. This not only boosts the life expectancy of the equipment however also improves total efficiency. Moreover, maintaining detailed maintenance records is essential. These logs give insights into repeating issues and aid in preparing future upkeep activities extra effectively.
Verdict
Customized packaging equipment repair service services play a vital duty in enhancing operational performance and reducing downtime by straightening repair services with details process dynamics. These personalized options utilize high-grade, suitable components and proactive upkeep plans to expand equipment lifespan and optimize performance. By promoting close connections between organizations and company, customized solutions improve solution quality and lower prices. Picking the right service provider makes certain the effective implementation of these options, eventually leading to significant long-term benefits for organizations.
In today's competitive market, services must guarantee their product packaging operations run perfectly, and tailored repair service solutions for equipment are pivotal in attaining this.To effectively resolve the fixing and upkeep of product packaging devices, it is paramount to acquire a thorough understanding of your devices requires.Personalized fixing services provide a tailored approach Full Report to repairing and maintaining packaging tools, ensuring options that fit the special demands of each service.Effective tools upkeep methods are as important as selecting the appropriate service copyright when it comes to maximizing the life expectancy of product packaging equipment.Customized packaging devices repair work services play a vital function in improving operational effectiveness and reducing downtime by lining up fixings with certain operations dynamics.